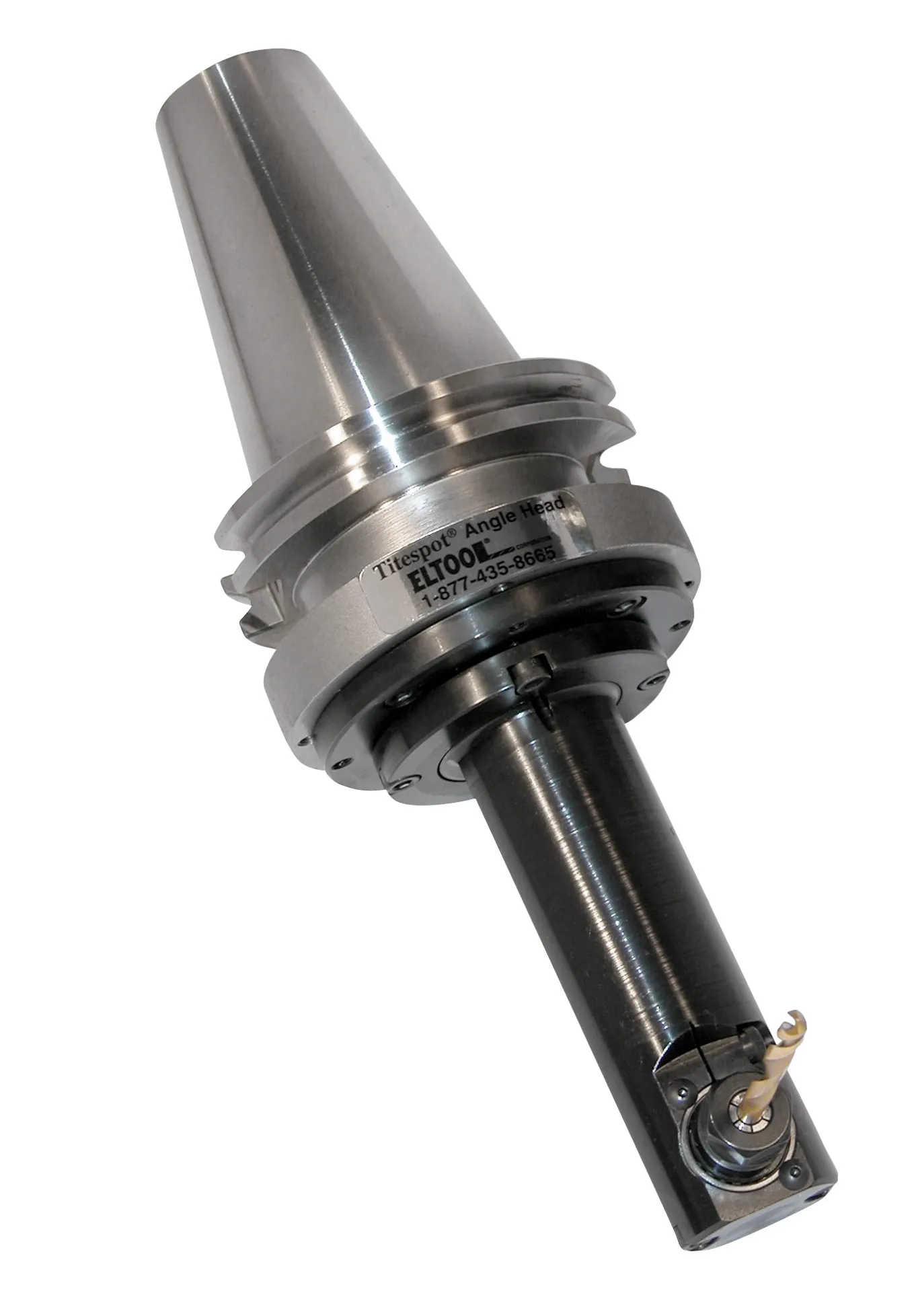
Dimac News
Titespot® Angle Head provides solution to manufacturer caught in a tight spot.
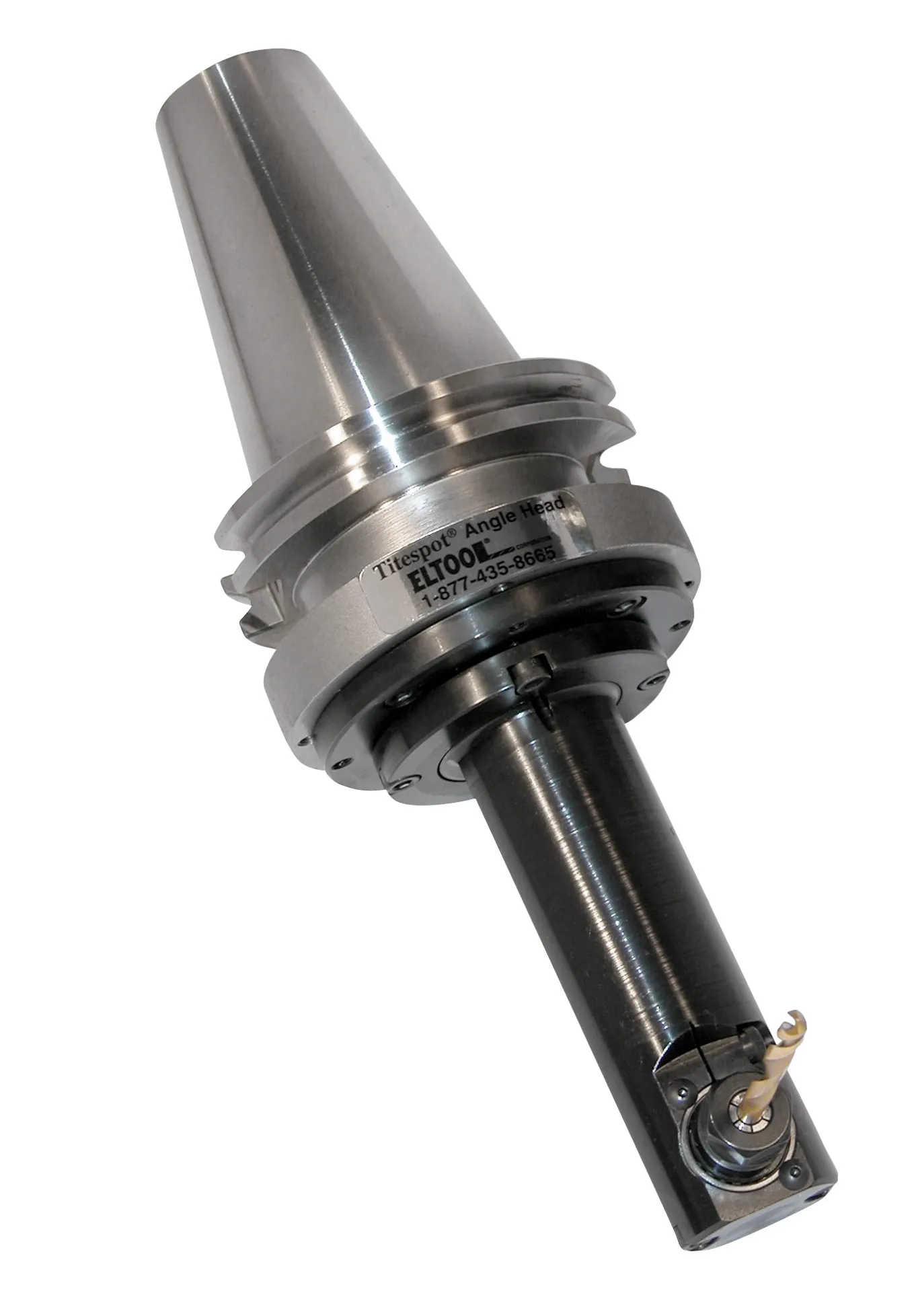
Dimac Tooling, Australia and New Zealand's leading supplier of accessories and workholding solutions for CNC milling and CNC turning machine tools, is the exclusive agent for Eltool products and its range of Titespot® Angle Heads.For over 15 years Titespot® Angle Heads have offered a cost effective alternative to EDM and mechanically driven angle heads, particularly where multi-position radial machining and/or machining in small bores or cavities is required.Because spindle rotation is not required to power the angle head, the machine spindle becomes an indexer, allowing multi-position machining with one head and one set-up. The smallest head in the range can machine radially in bores down to15.9mm in diameter.Recently, a US based CNC manufacturer, Antron Engineering and Machine Co. came upon the challenge of milling a long interrupted slot in a small-diameetr bore for a prototype part.Added complexity was due to the fact that they had to effectively and consistently machine features in a cylinder housing made of 7075 aluminium. The componentwas part of a pump unit that runs the hydraulics for the controls and engine in an aircraft – a crucial component that could not afford to fail.The only option initially appeared to be planing or building a motorised head that powered a gear driven tool and fit that into the machine tool spindle – not an ideal solution due to cost and question marks over its effectiveness and accuracy.After looking at other options the company came across Eltool Corporation based in Cincinnati and after viewing the website came across the Titespot® Angle Heads range which relies on high-pressure coolant to drive an integral, positive–displacement ball piston motor.The motor powers a drive shaft, which in turn drives the head’s spindle while exhausted coolant is directed at and through the cutting tool. Because the angle head has its own power a machine spindle can function as an indexer allowing multiple-position machining with one head and set-up.The product appeared to be the solution that Antron were looking for and went ahead and bought a Titespot® Angle Head. Needless to stay it has performed perfectly producing the required part in a short time frame with absolute precision.A company spokesman said that not only had it provided significant cost savings but crucially provided process certainty – instead of 100% of the time not knowing if the machined part would be good or bad.“Quite literally Titespot® Angle Heads can get manufacturers out of a tight spot when it comes to cost effective and accurate machining where multi-position radial machining and/or machining in small bores or cavities is required,” Dimac’s Managing Director Paul Fowler said.“The other major benefit is that we are confident the Titespot® Angle Head will be able to be utilised for other jobs. You don’t need to purchase a completely new angle head for different applications. Instead you can buy a different drive shaft and tool assembly for about half the cost because the hydraulically powered motor is universal for all the different attachments,” Mr Fowler went on to say.Dimac has over 30 years experience in CNC machine tool accessories and are agents for many highly respected brands such as Kitagawa, Cooljet, Reven and Eron. The company also manufactures soft and hard jaws in their own CNC equipped machine shop.“Like all the products we sell, Eltool Titespot® Angle Heads are supported by the full back up and support of Dimac technical personnel to ensure the right product is specified and operates at optimum performance,” Mr Fowler concluded.