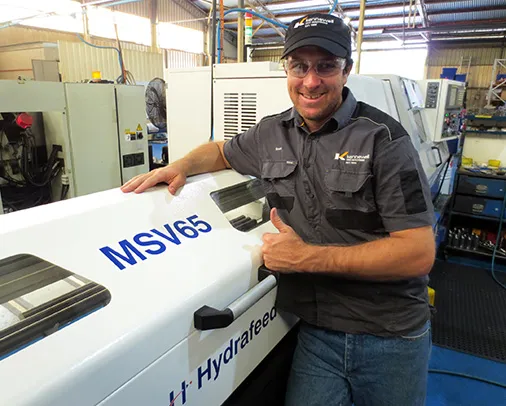
Dimac News
Dimac’s Hydrafeed Barfeeder lifts productivity at Kennewell CNC Machining.
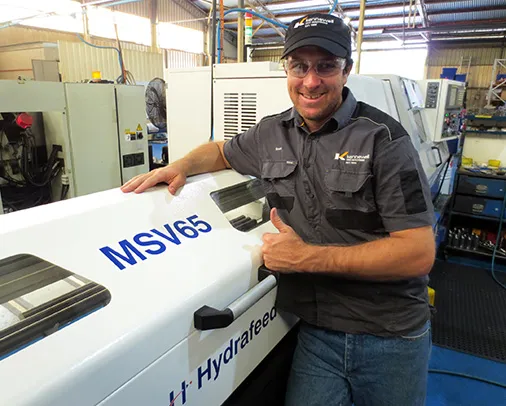
Kennewell CNC Machining, a contract machine shop in South Australia which specialises in small batches, manufactures everything from parts for agricultural machinery to high end motorsport and tattooing equipment.It is also heavily involved with the production of prototype parts to assist companies bring products to market.Established in 1995, the company has steadily grown and now has a total of twelve staff working over two shifts.Owner Brett Kennewell and Leading Hand Brett Klose recently invested in a servo-driven Hydrafeed Barfeeder from Dimac, in order to retrofit to an existing CNC lathe and replace the existing pneumatic unit that had come with the unit.
“I really don’t like pneumatic equipment; the barfeeder we had has been unreliable and because it ran on compressed air was expensive to run,” said Mr Kennewell.
“Dimac’s service was also a breath of fresh air. Competitive suppliers seemed reluctant or unable to bring in a machine for me to test, but Paul Fowler of Dimac brought the Hydrafeed Barfeeeder in and demonstrated the unit. It certainly ticked all the boxes,” Mr Kennewell went on to say.
“Our old barfeeder had to be monitored constantly, so was very unproductive.The key benefit of the Hydrafeed Barfeeder is that it has increased my productivity by allowing me to run the machine unattended; it’s essentially given our existing CNC lathe a new lease of life,” Mr Kennewell added.
Hydrafeed U.K. developed a very user friendly unit with an additional productivity benefit over other barfeeders on the market. Once you’ve set a bar size and saved the setup, you are not required to open the cover again. One simply calls up the program from the touch screen and the HydraFeed will set itself on centreline automatically thanks to the servo drive bar lifter mechanism.
“One of the other features is that the Hydrafeed is very easy to use so it doesn't take long for other staff members to become proficient at operating it,” explained Mr Kennewell.
Standard features include servo control, fully automated set-up through a user friendly HMI screen and the versatility to accommodate different bar diameters and lengths including random bar lengths. A wide variety of models are available to suit any application.Kennewell also benefitted from the one-on-one training that Dimac provided, to ensure the barfeeder was installed correctly and operated at optimum performance.
“I would recommend the Hydrafeed Barfeeder without hesitation to any company,” Mr Kennewell summed up.
Dimac Tooling, Australia and New Zealand's leading supplier of accessories and workholding solutions provides a range of cutting edge equipment designed to assist companies increase their efficiency and productivity. The company also manufactures soft and hard jaws in their own CNC equipped machine shop in Dandenong South, Victoria.